
Corrosion & Erosion Management
Viking is an industry leader with the extensive knowledge and experience to identify project-specific corrosion control alternatives during design, installation and operations. As a vital part of integrity management, corrosion control options are evaluated considering multiple aspects of the system and troubleshooting of ongoing issues are determined.
Our Services
Coating & Insulation Services
Corrosion & Erosion Management
Cathodic Protection Design, Installation & Surveillance
Corrosion Management
Viking’s capabilities in corrosion engineering are well recognized within the industry and have played key roles in hydrocarbon developments worldwide.
The Corrosion, Materials and Integrity (MCI) Team for oil and gas developments and water and gas injection systems and other process facilities forms one of Viking’s core engineering services.
The MCI Team is involved at all stages of project development (Concept to Operations) and offers a significant interface with chemical systems engineering, flow assurance, operations, installation, and surveillance teams.
The Asset Integrity team develops whole-life cost solutions to corrosion and materials issues for downhole, subsea, flowlines, pipelines and process facilities.
Protective Coatings & Linings
Protective coatings are essential to preserving the integrity of steel piping, pressure vessels, and tanks. And expert technical assurance is critical to the selection, installation, inspection, and maintenance of protective coatings and linings. Viking can provide the expertise to help you get the performance you need.
The cost of coatings maintenance is high. An operator is likely to spend millions of dollars on coatings when fabricating a new facility only to spend millions more each year on fabric maintenance while still falling behind. Ultimately, external corrosion leads to expensive replacement of steel and even more costly LOPCs.
Viking’s protective coatings specialists can turn a losing battle with corrosion into a winning program of action. With attention paid to asset lifecycle, the coating process, and scope prioritization, we can get your coatings working for you.
Upstream, midstream, or downstream, new fabrication or fabric maintenance, we’ll work to ensure you get the most from your investments in protective coatings by navigating critical elements such as:
Design & Fabrication Issues Affecting Coatings
Requirements and Methods for decontamination (Oil, Grease, Salts)
Selection of Preparation Methods (Wet and Dry Abrasive Blasting, UHP Waterjetting, Dry Ice, etc.)
Selection of Appropriate QC Testing for All Process Stages
Coating Product Selection by Service Requirements
Corrosion Under Insulation (CUI) Prevention and Remediation
Alternative Coatings (Metallization, Wraps, Moisture-cured Urethane Systems, Under-water coatings, Thermoplastics)
Selection and QA/QC for Linings (Internal Coatings) for Piping, Tanks, and Pressure Vessels
Services we provide include:
Consultation
Painter/Blaster Qualification & Competency Training
Inspection
Vendor Surveillance
Project Management
Safety & Quality Auditing
Writing and Revising Maintenance and New-build Coating Specifications
Program Creation and Optimization (Cost Analysis)
Failure Analysis
Over half of all LOPCs are caused by external corrosion. Investments in protective coatings are significant, but the cost of corrosion is much higher. Together, we can do it right and make it count.
Corrosion & Erosion Management
Corrosion and Erosion Modeling
Process modeling and simulation (HYSYS/OLGA combined models)
Customized Corrosion and Erosion Management Programs
Corrosion and Erosion Monitoring Systems – Design, Implementation, and Surveillance
Corrosion Under Insulation (CUI) Prevention, Detection, and Mitigation
Cathodic Protection Design, Installation & Surveillance
Viking provides detailed engineering support for cathodic protection design. This also includes the qualification of coating applicators and anode manufacturing facilities. Associated responsibilities include supporting flowline and equipment installations for deepwater facilities and the post‐installation surveying of equipment.
Viking’s industry-renowned expertise on cathodic protection (CP) provides the right solutions for CP design, installation, maintenance and monitoring services. Viking’s well-established knowledge and significant experience in design in the areas of:
CP System Design, Specification, Review and Validation
Attenuation and Interference Studies
Anode Specification and Vendor Facility Inspection & Auditing
System Design Monitoring and Inspection Strategies During Field Design
Inspection and Auditing During Fabrication And Vendor Qualification including Welding, Coating, Anode Chemistry, Positive Material Identification
Corrosion Management
Material selection recommendations on a project are supported and supplemented by comprehensive corrosion, erosion, and souring reviews using various software packages.
Our engineering support also extends to developing and coordinating corrosion testing and inhibitor qualification programs, to validate both material and chemical selection choices. This exercise also involves the recommendation, specification and commissioning of corrosion probes and sand monitors. In addition, the team extends its expertise to help develop and implement surveillance programs to ensure ongoing asset integrity through the life of the development.
Corrosion engineering management also extends to the troubleshooting of corrosion problems on operating facilities. This includes the management and mitigation of Carbon Dioxide (CO2), Hydrogen Sulfide (H2S) and microbiologically induced corrosion (MIC) modeling and failure mechanisms.
Downhole & Subsea Materials Selection and Qualification Erosion/Corrosion Risk Assessment and Modeling Scaling Studies (Formation Risk, Removal and Mitigation Strategies)
Topsides materials Corrosion Monitoring, and Erosion Monitoring Systems
Risk-Based Assessment and Inspection Planning Troubleshooting Corrosion Problems on Operating Facilities
Consult Our Specialist
Related Resources
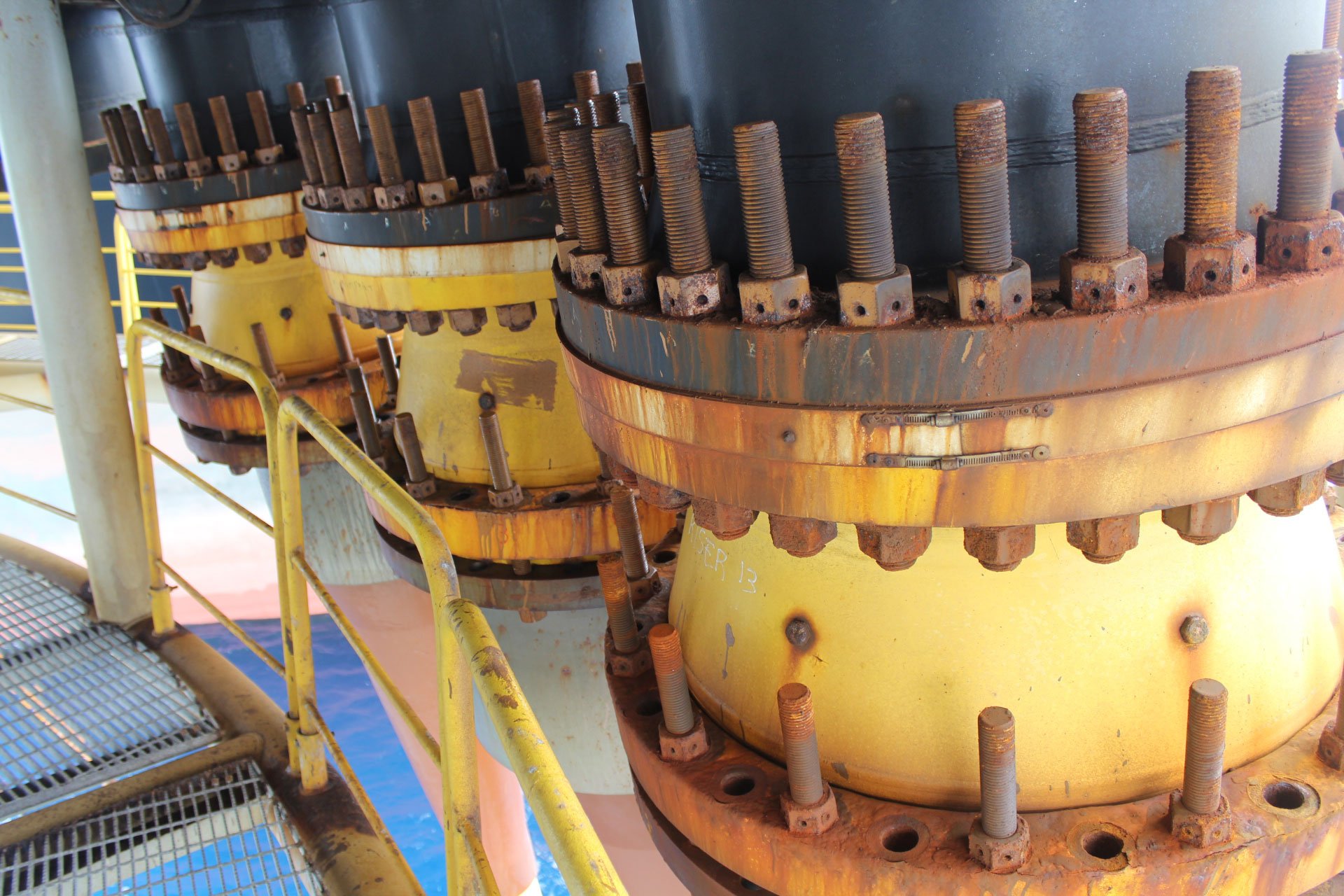