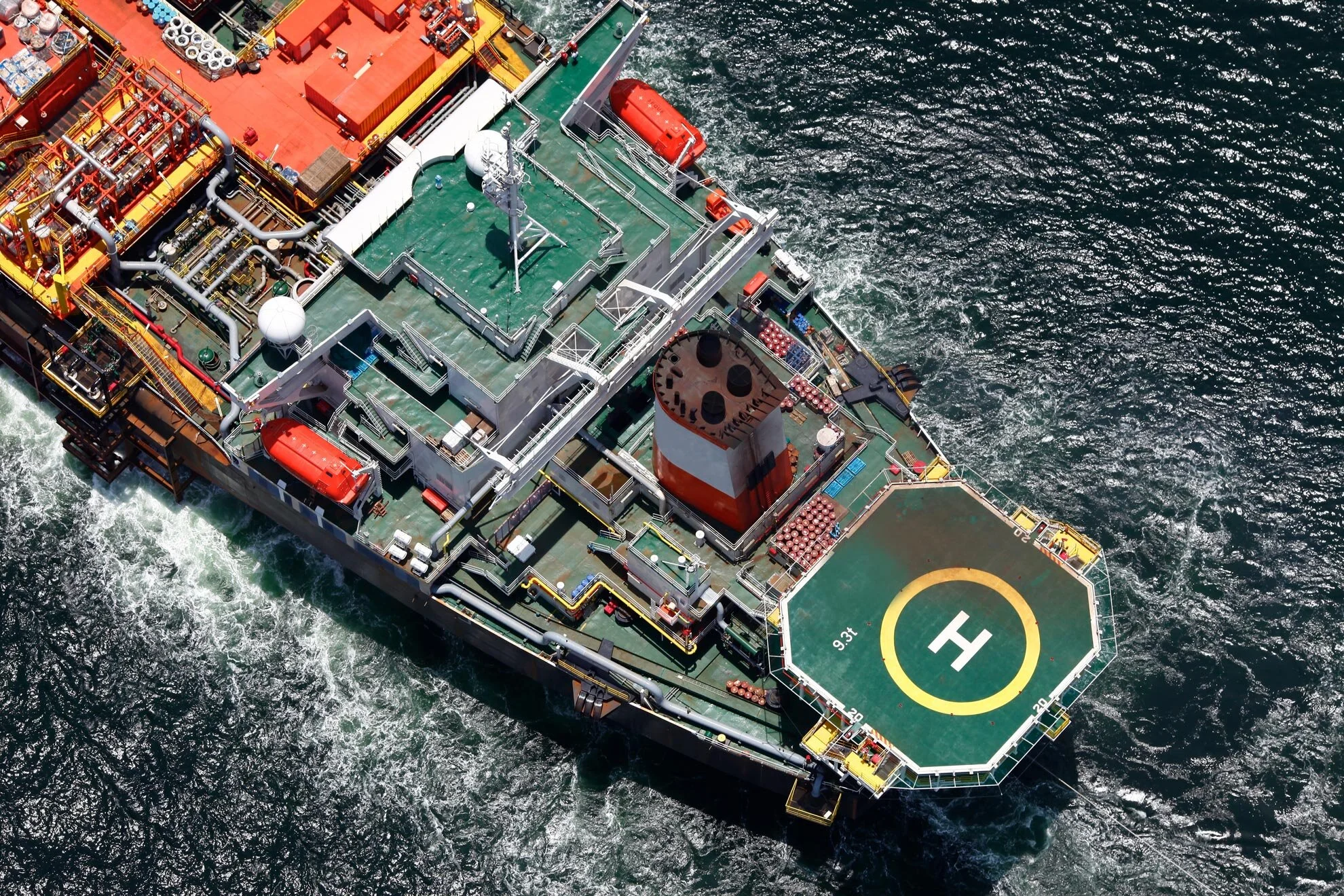
Project Experiences & Successes
6 Critical Steps to Create a Successful Frac Program & Mitigate Well Failures: A Case Study
An independent oil operator experienced four back-to-back casing failures in his Oklahoma shale program. These current failures and setbacks were eating into his budget and eroding stakeholder faith in the ability to complete wells.
His initial comment was, “I’m not getting any sleep – I need some help. You’ve got to help me stop the leaks!”
Shell - Ursa Princess Waterflood Commissioning
GATE provided seawater treating equipment process, materials, corrosion, chemical, and commissioning / start-up expertise. The scope included shaping the design of the seawater treating equipment and providing commissioning leadership and start-up expertise. The equipment included a Minox and Sulfate Removal Units.
BP Pipeline - Flow Assurance Management Program (FAMP)
BP Pipeline oversees the operation of 9 total oil and gas export systems from more than 20 different platforms in the GoM. The pipeline systems transport almost half-million barrels of oil and hundreds of MMSCF of gas daily from the producing platforms to onshore processing facilities.
The FAMP has been developed for BP Pipeline assets to ensure proper working of the high volume systems by organizing and delegating between operators, facilities, laboratories and onshore offices. By facilitating the review of system performance and operation, this information provides the basis of a continuous improvement approach.
Chevron - Materials & Corrosion Support
As part of the scope of work, GATE was commissioned to develop two comprehensive, user-friendly screening tools to guide subsea flowline materials selection decisions for wet gas and waterflood during concept selection and design using field specific data.
Shell - Rocky Umbilical Post-Mortem
GATE undertook an investigation into recovered, decommissioned equipment to determine both the cause of failure and investigate integrity of components that may not have failed. This information has proven invaluable to operators who can base the performance of other equipment of a similar type and construction in a similar environment. This was significant as the recovered materials ranged from the mud-line, to sea surface and topsides.
Shell EPP Support - Cathodic Protection
GATE provides Shell with cathodic protection design support for all their subsea projects. This includes coating selection (anti-corrosion and flow assurance) and qualification, which also involves interfacing with the coating yard. An important aspect of this operation is carrying out comprehensive quality audits of anode foundries and coating plants around the world.
Williams Pipeline - Tahiti Gas Export Line
GATE determined the risks and mitigation of risk associated with wet parking and flooding of a gas export pipeline with unfiltered seawater. The key concerns are corrosion due to microbes, oxygen corrosion, and drying to prevent hydrate formation when the pipe goes into service.
Kerr McGee - Red Hawk Sand Management Program
GATE undertook erosion and corrosion modeling in the flowline to develop sand production allowance and an erosion corrosion risk assessment. From this, a maximum rate of gas production that will allow the asset to maintain it design life was determined. This enabled the operator to safely increase production by 25% to without additional risk to the asset thereby increasing the Net Present Value of the asset.
Remaining Life Assessment Of Subsea Jumpers, Flowlines & Risers
GATE was engaged to evaluate the current condition and remaining life of the subsea jumpers and flowline of a deepwater oil and gas facility in the Gulf of Mexico.
The subsea field, which was comprised of multiple oil wells, was produced at a Tension Leg Platform (TLP) with a nominal capacity to produce 100,000 barrels of oil and 50 million cubic feet of gas per day. The subsea and topsides facilities were designed to operate with an expected maximum carbon dioxide (CO2) concentration of 0.15 mole percent from any given producing well.
Third Party Facilities Assessment
As part of a recent asset acquisition due diligence, GATE was asked to deliver a third party review of the condition of the asset and remaining production life of a floating production system and a fixed jacket.
GATE developed a standardized work process to evaluate the current condition, potential production bottlenecks and future operating expenditure (OPEX) associated with the brown-field producing asset.
Riser Life Extension Review
The review of the remaining cathodic protection (CP) life of a Gulf of Mexico tension-leg platform (TLP) was undertaken to evaluate the ability of the current systems to support a 20-year life extension. At the same time, the opportunity to include non-destructive riser testing into the life extension program was also identified.
Inspection Of Mill Certificates
During the fabrication of the subsea boarding valve skid for a major offshore platform in the Gulf of Mexico, the fabricator purchased several large forgings. These large forgings, from 8” to 12” in diameter, were to be machined into block valve bodies rated to 15,000 psig. As part of the agreed-upon Inspection and Test Plan, the mill certificates for the forgings were reviewed by the fabricator and by the company inspector.
Steam Plant Piping Corrosion
A steam generating plant supporting an associated thermal recovery project in the Middle East was experiencing through-wall corrosion of carbon steel lines. In some locations this was aggressive enough to corrode through replacement piping in as little as two months.
Global, Comprehensive Materials, Corrosion & Integrity Support
A client operating domestically and internationally needed expert technical support for materials and corrosion control. Their senior management came to Viking for a proposal to provide a variety of consultancy services to cover the following essential needs: materials selection, failure analysis, corrosion monitoring, technical assurance for procurement, and risk assessment.
Well Integrity
We partnered with a major operator to develop and implement customized strategies to ensure well facility integrity by mitigating unforseen failures to maximize safety and uptime while minimizing cost.
Onshore Asset Integrity Management
GATE was consulted to identify the source of unexpected levels of H2S that had been detected in the central processing facility. Ultimately, GATE was able to determine that multiple operational issues needed to be addressed to mitigate the high levels of H2S in the processing facility, rather than the H2S naturally occurring in the reservoir.
Life Extension Study
A large and complex offshore field in the Middle East was suffering from multiple leaks due to corrosion in the presence of high levels of CO2 and H2S in the production, seawater injection, aquifer water injection and produced water injection systems. This was resulting in excessive chemical injection expenditures and was impacting field revenues and uptime. The large, shallow water field consisted of several hundred wells and a complex hub and spoke infrastructure.
Inspection Plan Development For Mothballed Equipment
A South American operator developed plans to return a sulfur recovery unit to service after an initial ten years of service and a further ten years of mothballing due to changes in field production requirements.
The corrosive nature of molten sulfur, carbon dioxide and hydrogen sulfide in the unit, coupled with the expectation of a less than optimum preservation strategy in a littoral offshore environment, generated a large set of integrity risks that needed to be evaluated to determine the feasibility of repairing and reinstating the system for a further ten years of service.