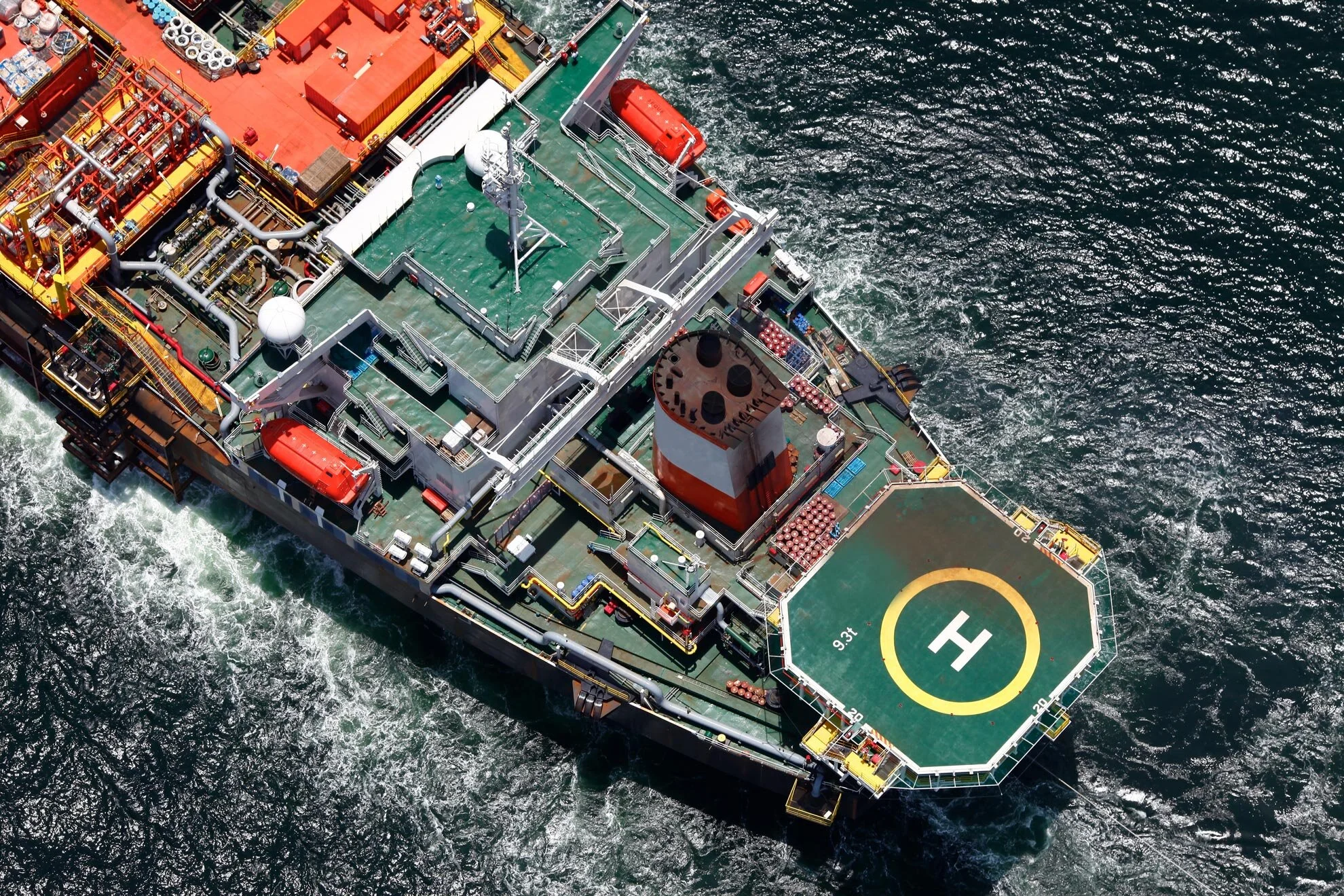
Project Experiences & Successes
Noble Energy – Hagit Terminal
GATE Energy provided systems completion and commissioning execution services provided for onshore gas loading terminal near Haifa, Israel. Planning and Systems Completion efforts primarily located in Houston, TX with regular trips to Israel.
Flint Hills Resources / KBR – West Plant Domestic Crude Project / Tier III LSG Project
GATE Energy provided commissioning services for refinery upgrade project near Corpus Christi, TX.
Juniper GTL – Gas to Liquids Plant / Wax Upgrading
GATE Energy provided full commissioning planning and execution for GTL plant in Westlake, LA.
Koch Industries / KBR – Enid Expansion Project
GATE Energy provided full commissioning and start-up services for fertilizer plant project in Enid, OK.
Noble Energy – Keota Gas Plant
GATE Energy provided client commissioning oversight, Commissioning Manager/Engineer for NGL gas plant in Colorado.
Steam Plant Piping Corrosion
A steam generating plant supporting an associated thermal recovery project in the Middle East was experiencing through-wall corrosion of carbon steel lines. In some locations this was aggressive enough to corrode through replacement piping in as little as two months.
Global, Comprehensive Materials, Corrosion & Integrity Support
A client operating domestically and internationally needed expert technical support for materials and corrosion control. Their senior management came to Viking for a proposal to provide a variety of consultancy services to cover the following essential needs: materials selection, failure analysis, corrosion monitoring, technical assurance for procurement, and risk assessment.
Onshore Asset Integrity Management
GATE was consulted to identify the source of unexpected levels of H2S that had been detected in the central processing facility. Ultimately, GATE was able to determine that multiple operational issues needed to be addressed to mitigate the high levels of H2S in the processing facility, rather than the H2S naturally occurring in the reservoir.
Inspection Plan Development For Mothballed Equipment
A South American operator developed plans to return a sulfur recovery unit to service after an initial ten years of service and a further ten years of mothballing due to changes in field production requirements.
The corrosive nature of molten sulfur, carbon dioxide and hydrogen sulfide in the unit, coupled with the expectation of a less than optimum preservation strategy in a littoral offshore environment, generated a large set of integrity risks that needed to be evaluated to determine the feasibility of repairing and reinstating the system for a further ten years of service.