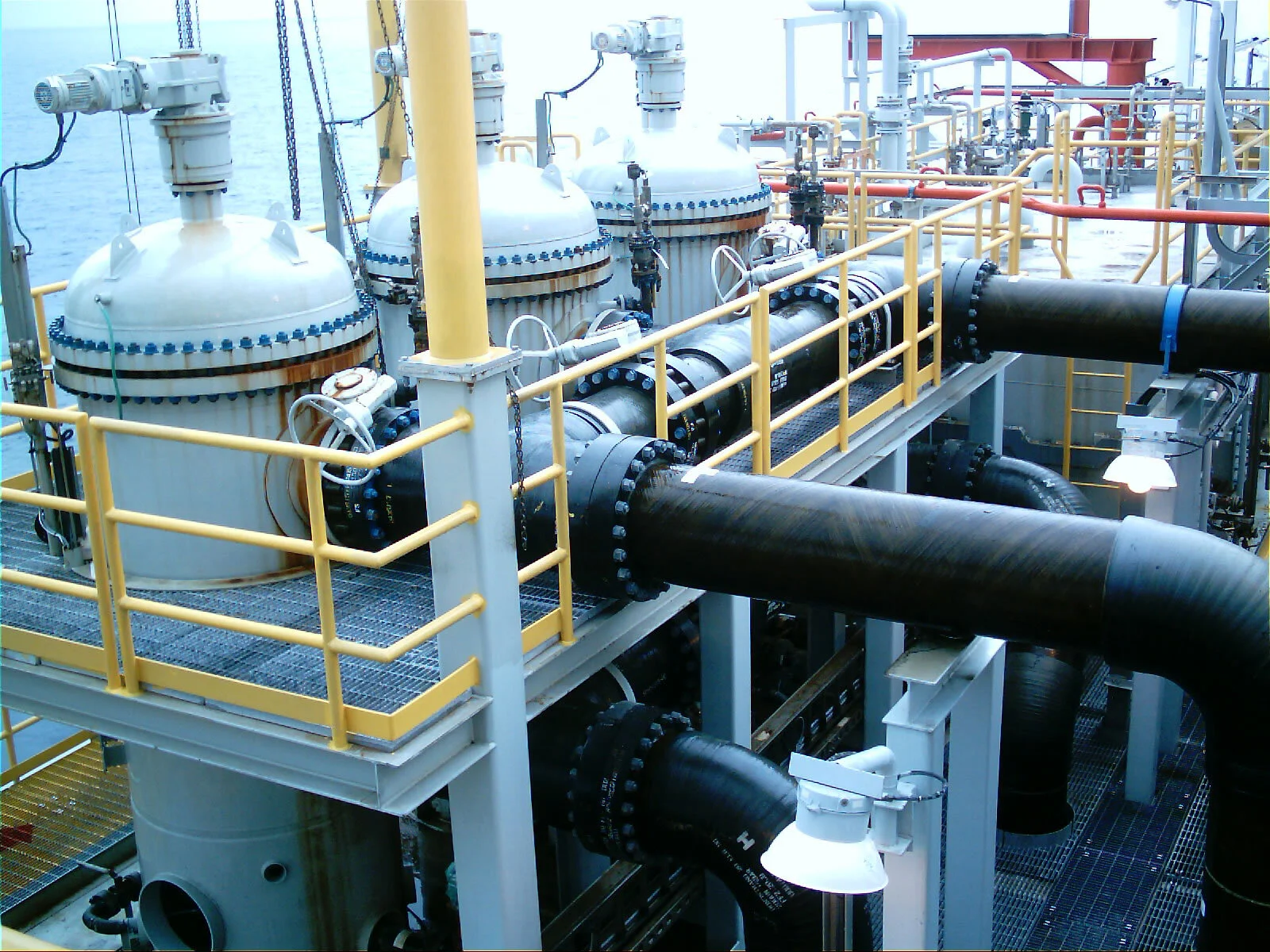
Water Injection System Design, Optimization & Troubleshooting
Interfacing with core waterflood groups involving team members from reservoir, completions, subsea, flowlines/risers, and topsides to arrive at a design is crucial.
Our Services
Water Injection System Design & Selection
Material Selection & Corrosion Modeling
Souring & Scaling Modeling
Thermal & Fracture Modeling
Optimization & Troubleshooting
We focus our core areas of expertise of materials, corrosion, production chemistry, and flow modeling coupled with field experience.
The primary focus of the Viking Water Injection Team is to provide systems engineering solutions to waterflood design, commissioning, and system operability. Our involvement in multiple water injection system startups allows our engineers to arrive at a design which will achieve reservoir engineering expectations.
The work process begins with understanding the water chemistry – which drives the souring, scaling, and corrosion aspects of the design. Understanding the voidage replacement requirements, expected availability of the system – the topsides throughput can be arrived at, and then working with completions a topsides pressure estimate is calculated. This information begins to form the basis of design in which novel technologies can be identified such as high pressure pumps or Oxygen Removal units.
Overall, Viking is instrumental in bringing definition to the project based on system engineering principles, time tested production chemistry, true offshore commissioning & startup experience, and operational flow assurance techniques.
Read more about our Water Injection System Design Services below:
Water Injection System Design & Selection
The design of water injection systems is a key aspect of optimizing the economic return of any development. This is particularly true of systems that are placed on floating production systems, where weight, space and power requirements may be limited.
Viking provides expert advice to many deepwater assets regarding the layout of their water injection systems, including aspects such as the feasibility of commingled seawater and produced water injection, options for seawater lift, filtration technologies, sulfate removal, low salinity seawater injection, oxygen removal, process arrangement and injection pump selection.
Such considerations are based around the physical constraints of each project, the relationship between capital and operational expenditure for each option, and the overall system reliability and field economics for the development.
Water Injection Material Selection & Corrosion Modeling
Materials selection in water injection system needs to balance many factors to obtain an optimum solution. Through the processing system the type and magnitude of integrity threats are constantly changing, resulting from factors such as oxygen corrosion, acid corrosion, erosion, biofouling, microbial activity, under-deposit corrosion, and chemical incompatibility.
The impact of a loss of containment on system uptime, operator safety, company reputation and overall production also changes at various points in the system and for different assets, where specific assets will also require different balances between upfront capital expenditure and later operational expenditure.
Viking uses our systems engineering, materials and integrity management, commissioning and operating knowledge of onshore and offshore water injection systems around the globe to reach a solution that is optimized to the need of each Client and each asset. This can transcend engineering, where aspects such as tax law differences between capital and operating costs can drive different materials selections in different parts of the world.
Water Injection Souring & Scaling Modeling
Viking uses commercial reservoir modeling packages to undertake evaluations of water injector placement and to estimate and optimize water injection performance. This is often linked to services such as injection system design and optimization and the management of scaling and souring impacts as a result of water injection.
One of the biggest uncertainties when planning water injection is the subsequent impact on production operations. Major challenges Include:
Health and safety management
Blockage of flow and the associated deferred production.
Remediation costs from scale deposition.
The impact of reservoir souring on materials selection and performance.
Product value
Viking specializes in understanding and managing production issues related to souring and scaling risks. Viking provides risk assessment tools to monitor and evaluate reservoir souring, alongside the use of industry-standard models for scale modeling and three-dimensional reservoir modeling. We develop total quality assurance strategies specific to your needs.
Water Injection Thermal & Fracture Modeling
Injection into hot and high-pressure deepwater reservoirs is often constrained by concerns associated with fracture propagation.
By modeling fracture behavior to optimize water injection flow rates and pressure, it becomes possible to control fracture propagation where this supports injection and to avoid fracture generation where matrix injection results in the most efficient means of injector operation.
Water Injection Optimization & Troubleshooting
Injection program optimization encompasses multiple disciplines including reliability and maintenance, asset integrity management, production chemistry, operations and reservoir engineering.
Viking’s multidisciplinary approach to solving engineering and operational challenges readily lends itself to such cross-disciplinary collaborative efforts and often provides the core of initiatives to lower costs, increase up-time and increase incremental production due to water injection operations.