Chemical Vendor Qualification & Selection
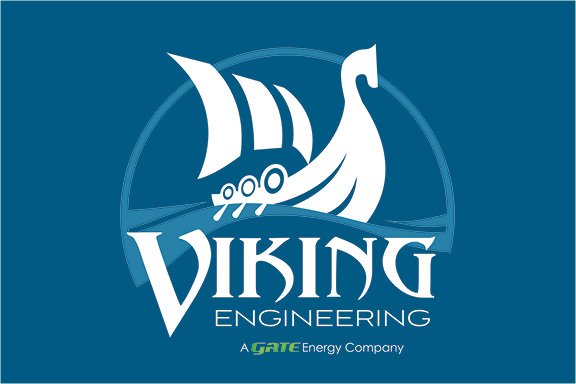
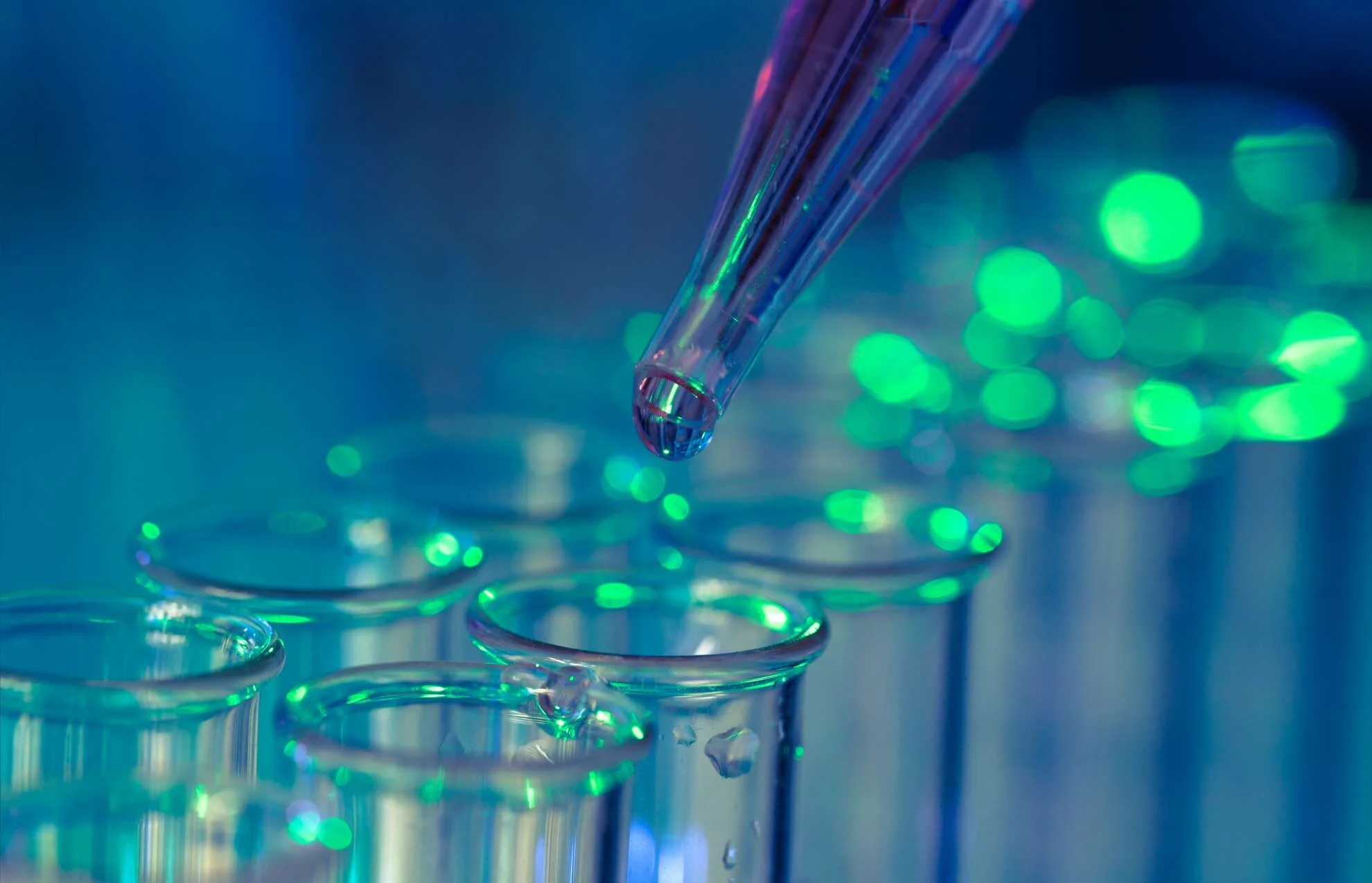
Viking’s Chemical Vendor Qualification procedure for technical and business compliance provides a transparent procedural overview of the process. This clear perspective provides well-defined roles and responsibilities for each associated member associated with the qualification process.
Chemical Vendor Qualification & Selection
Viking manages chemical vendor qualifications and selections, which includes:
Development of chemical functional and testing requirements
Organizing vendor site visits
Development of a comprehensive summary of the qualification results for each chemical vendor.
Viking is proud to possess one of the best interface management teams in the industry.
Resources
Consult a Specialist
The objective of this GATEKEEPER is to provide a high-level overview of the model commonly used in the industry to estimate the wax deposition.
The design and development of a viable, robust wax management strategy relies upon the economical evaluation of available management techniques.
Wax management strategies developed during Front End Engineering Design (FEED) can mitigate or perhaps even prevent these costs. The goal of this GATEKEEPER series is to provide high-level insight into the planning, execution, and maintenance of wax management strategies.
This GATEKEEPER discusses the various bacteria testing options that are available, which can be used to validate MPN results, as well as the mitigation and remediation techniques that can be used to decrease the probability or severity of MIC to pipeline infrastructure.
This GATEKEEPER provides an overview of the decisions which are the truly important outcomes from this process, and outlines the risks we incur by setting our scale management and associated field design philosophies early in the life of a project.
This GATEKEEPER will discuss the key physical and chemical characteristics of each production chemical that must be evaluated prior to use in a subsea production system.
The amine selected, as well as the concentration of the solution used, will result in different selectivity of H2S over CO2, mole-to-mole acid gas loading, and degradation of the amine.
Corrosion modeling is a vital tool in the pre-Front End Engineering Design (pre-FEED), FEED, and operational stages of the life of pipeline and equipment systems.
Proper sizing of the flowlines and risers coupled with optimal choking and gas-lift will greatly reduce the risk of slugging and help in efficient management of slugs throughout the life of the field.
Paraffin precipitation and deposition in flowlines and pipelines is an issue impacting the development of deepwater subsea hydrocarbon reservoirs.
While one test cannot give comprehensive results, a combination of testing including genetic testing will be able to provide a more reliable and complete picture of the bacteria in the system than the use of MPN alone.
This article compares the common approaches to specifying chemical cleanliness and subsequently presents high-level guidance that can be used to select appropriate quality control criteria for those chemicals deployed through long-distance umbilicals to subsea and sub-surface injection locations
The objective of this article is to summarize the main requirements of the permit, identify changes from the previous permit, and call out edits between the draft and final issue of the permit as these pertain to the discharge of produced waters and other treated waters from offshore production and water injection facilities.
It is frequently necessary to displace the contents of a pipeline or umbilical tube (fluid B) with another fluid (fluid A). If we don’t use a pig to separate the liquids, there will be mixing at the interface (axial mixing). The mixing zone requires us to overflush the line to effectively remove fluid B from the line.
Asphaltenes are large, complex organic components present in the oil phase, along with resins, aromatic hydrocarbons, and alkanes (saturated hydrocarbons). Resins play an important role in stabilizing asphaltenes in crude oil. When the resins get destabilized, (under unfavorable pressure-temperature conditions) asphaltenes can agglomerate and deposit.
These work effectively on dispersed, O&G; however, these systems do not effectively remove water soluble organics (WSOs). Where WSOs exist in concentrations greater than 29 mg/l, conventional produced water treating systems cannot achieve GoM overboard discharge limits.
Methanol (MeOH) is widely used in multiple applications in the offshore oil and gas industry.
In subsea oil production systems, hydrate mitigation methods during steady state operation are almost always based around heat conservation.
Iron solid formation in the MEG regeneration system has been a recurring issue in wet gas pipeline systems.
In this 2-part GATEKEEPER series, we will discuss how centrifugal pumps work and what information is needed to determine the pump needed for a particular application.
In part 2, horsepower, efficiency and NPSH will be discussed which will lead to a final centrifugal pump selection.
Viking’s is engaged in all aspects of chemical-related technology for offshore and onshore facilities. The team focuses on production chemistry solutions, chemical injection system design and chemical umbilical commissioning.
Viking’s Chemical Vendor Qualification procedure for technical and business compliance provides a transparent procedural overview of the process.
Viking’s Chemical Systems team provides fit-for-purpose chemical injection systems for flow assurance specific needs to each project.
Viking’s Chemical Systems team determines what issues may cause an existing chemical system to not perform to the operators’ desired specifications and will deliver a course of action designed to mitigate these issues to ensure best performance.
