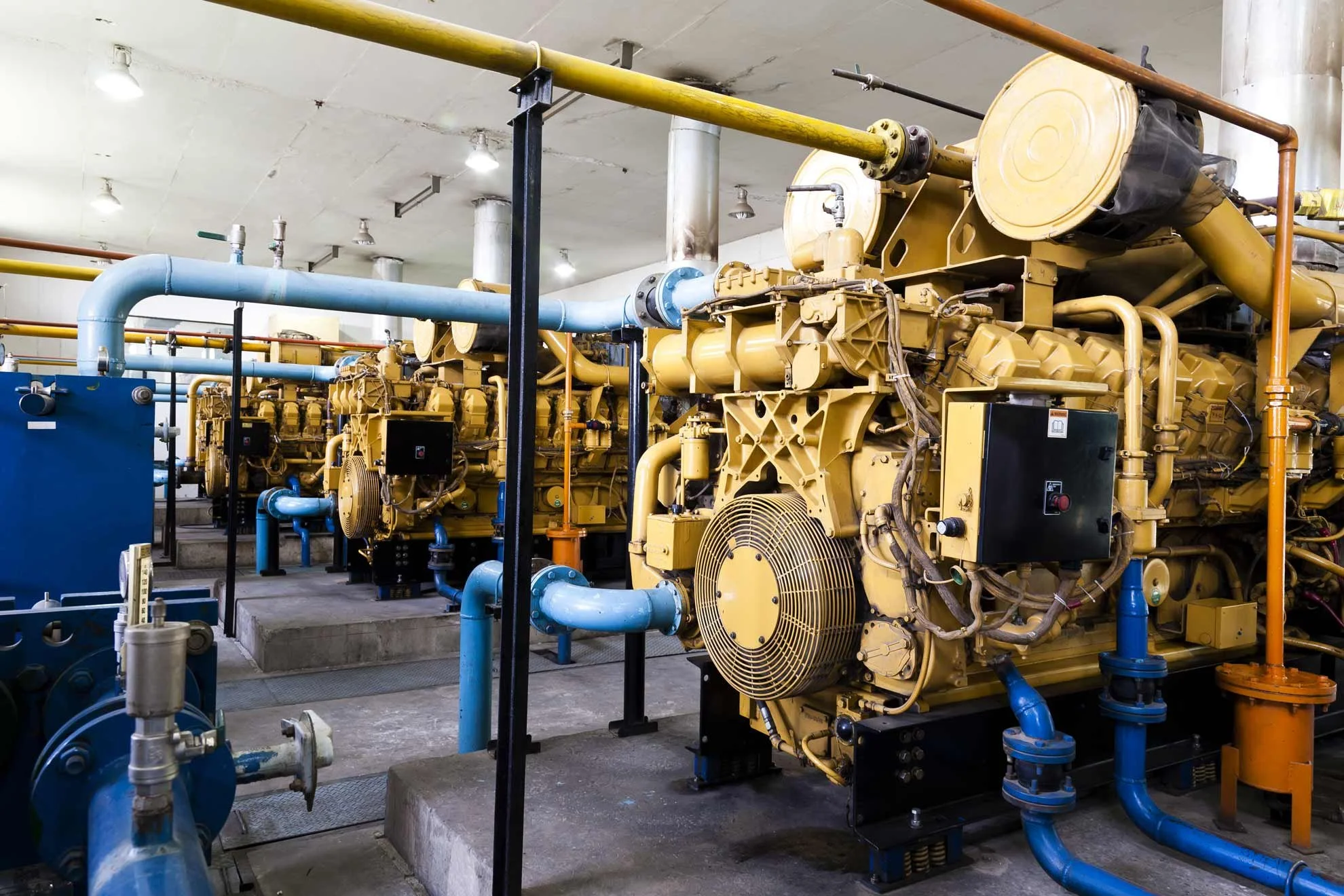
Chemical Flushing, Pickling, Passivation & Lube Oil Flushing
Our systems flushing and filtration team provides filtration units and flushing from downhole control lines, umbilicals, subsea trees, and topsides equipment offshore to control panels and compressor stations on land.
Our Services
Chemical Cleaning
Lube Oil System Flushing
Pickling & Passivation
Particle Counting Services
Filtration Equipment
Systems Flushing, Sampling & Analysis
Our filtration units are capable of high volume and/or low volume filtration and are designed to mitigate particle contamination.
Equally important, our field technicians are trained and competent on BlueFin’s approved process and procedures, which includes particle counting to the industries fluid cleanliness standards such as NAS 1638 and SAE AS4059. BlueFin’s field experts are prepared to meet you flushing and filtration needs.
Applications
Onshore and Offshore
Industries: Plants, Petrochemical, LNG, NGL
Maintenance and Turnarounds
Facility Upgrades and Expansions
New Construction
Control Oil Systems
Hot Oil, Subsea, Topsides Systems
Chemical Injection Systems
Well Head Control Systems
Chemical Cleaning
Amine Systems, Cooling Medium, Heat Medium, Steam Systems
Dry Seal Gas System Flushing
Hydro Blasting
System Filtration
Particle Count Reporting
Lube Oil System Flushing Services
Turbines
Compressors
Exchangers, Pumps
Seal Systems
Pickling & Passivation Services
Vat Dipping
Preservation
Particle Counting Services
Personnel Trained in Multiple Particulate Counting Standards
Our particle counting services and equipment includes:
BlueFin provides two types of fluid analysis systems, automatic particle counters and optical microscopes.
BlueFin personnel are trained in particulate counting standards such as NAS 1638, ISO 4406 and SAE 4059 rev. D and E.
BlueFin provides on site portable laboratory services.
BlueFin adheres by all lab procedures (APC or optical) such SAE ARP 598B.
Filtration Equipment
Pre-commissioning, Commissioning and Decommissioning
Maintenance
Fluid Sampling and Analysis
Fluids Polishing and Dehydration
Varnish Mitigation for Oil Systems
Pickling Fabricated Spools Prior to Installation
Filtration Control Manifolds For High Pressure, Multi-Line Flushing
Designed for high pressure, multiple line flushing and pressure testing manifolds are set up with twelve discharge and return ports with each port being isolated. Each port is equipped with its own sample port for individual fluid analysis.
BlueFin Model A manifold systems are designed for high pressure, multiple line flushing and pressure testing.
Filtration Units: NAS Filtration & Flushing of Bulk Fluids
Our bulk filtration unit is capable of NAS filtration and flushing of Bulk fluids with little to no pressure and can handle up to 125 GPM with 1-micron filter. Equipped with two stainless steel filter canisters rated for 100 psi, these canisters carry up to fifteen filter elements of any micron size desirable.
Piping size on our Bulk filtration unit is 3" for flow and is also equipped with a NU-FLO flowmeter on the discharge to measure gallons per minute and total gallons. It is also equipped with a sample port.
Bulk fluids are pumped through our filtration unit with either a 2" air diaphragm pump or 6 cylinder diesel pump.
Electric Filtration Units
EPU-A: Electric, High Pressure, Medium to Low Volume Flowrate
BlueFin Model EPU-A filtration units are designed for high pressure, medium to low volume flushing and testing of production, completion and subsea components and tools.
IPU-A: Electric, High Pressure, Medium to Low Volume Flowrate
BlueFin Model IPU-A filtration units are designed for high pressure, medium to low volume pumping of harsh chemicals.
EFU-B: Electric, Medium to Low Volume
BlueFin Model B filtration units are designed for medium to low volume flushing and testing of production, completion and subsea components and tools.
Pneumatic Filtration Units
PFU-A: Pneumatic, Small Footprint
BlueFin Model PFU-A filtration units are designed for low volume flushing and testing of production, completion and subsea components and tools.
The two-stage, multiple-line pneumatic filtration unit is rated for 15,000 psi and contains 4 separate test/injection and return points for multiple line filtration.
PFU-B: Pneumatic, 30,000 psi
BlueFin Model PFU-B filtration units are designed for low volume flushing and testing of production, completion and subsea components and tools.
The two-stage, multiple-line pneumatic filtration unit is rated for 30,000 psi and can produce up to 3 gallons per minute. It contains three (3) separate test/injection and return points for multiple lines filtration.
High Volume Filtration Units
HVU-A: High Volume, Small Footprint
BlueFin Model HVU-A filtration units are designed for high volume flushing and testing of production, vessels, tanks and large piping systems.
BlueFin Model A filtration units are designed for high volume flushing and testing of production, vessels, tanks and large piping systems.
Using Pall corporation NXA Absolute filters, BlueFin can provide filtration to customer specified NAS 1638, SAE 4059F or ISO 4406 classification.
BlueFin Model A filtration units are designed for high volume flushing and testing of production, vessels, tanks and large piping systems
Using Pall corporation NXA Absolute filters, BlueFin can provide filtration to customer specified NAS 1638, SAE 4059F or ISO 4406 classification.
BlueFin Model A Filter Skids are designed for low pressure with high flow capabilities to filter fluids used in umbilicals, subsea components, production and completion equipment and tools.
The diaphragm pump offers high volume delivery even at low air pressures with a maximum output of 13 gallons per minute with a flooded inlet. Pneumatic Filter Skids (PFS) can be used for filtering oil, water, glycols or other chemicals.
BlueFin Model B Filter Skids designed for low pressure with high flow capabilities to filter fluids used in umbilicals, subsea components, production and completion equipment and tools.
BlueFin Model A filtration units are designed for low volume flushing and testing of production, completion, and subsea components and tools.
The two-stage, multiple-line pneumatic filtration unit is rated for 15,000 psi and contains 4 separate test/injection and return points for multiple line filtration.
BlueFin Model B filtration units are designed for low volume flushing and testing of production, completion, and subsea components and tools.
The two-stage, multiple-line pneumatic filtration unit is rated for 30,000 psi and can produce up to 3 gallons per minute. It contains three (3) separate test/injection and return points for multiple lines filtration.
BlueFin Model A filtration units are designed for high pressure, medium to low volume pumping of harsh chemicals.
The HDP-72 Hammelamnn pump is built for continuous duty and is assembled with 22m diameter ceramic plungers, incorporating the packing less, “dynamic seal assembly” in the high-pressure end.
BlueFin Model A filtration units are designed for high pressure, medium to low volume flushing and testing of production, completion, and subsea components and tools.
BlueFin Model B filtration units are designed for medium to low volume flushing and testing of production, completion, and subsea components and tools.
Consult Our Specialist
President of BlueFin Pipeline, Process and Industrial Services
Responsible for the strategic vision of the BlueFin Pipeline, Process and Industrial field services business unit.
Phone: 337.551.6975
Related Resources
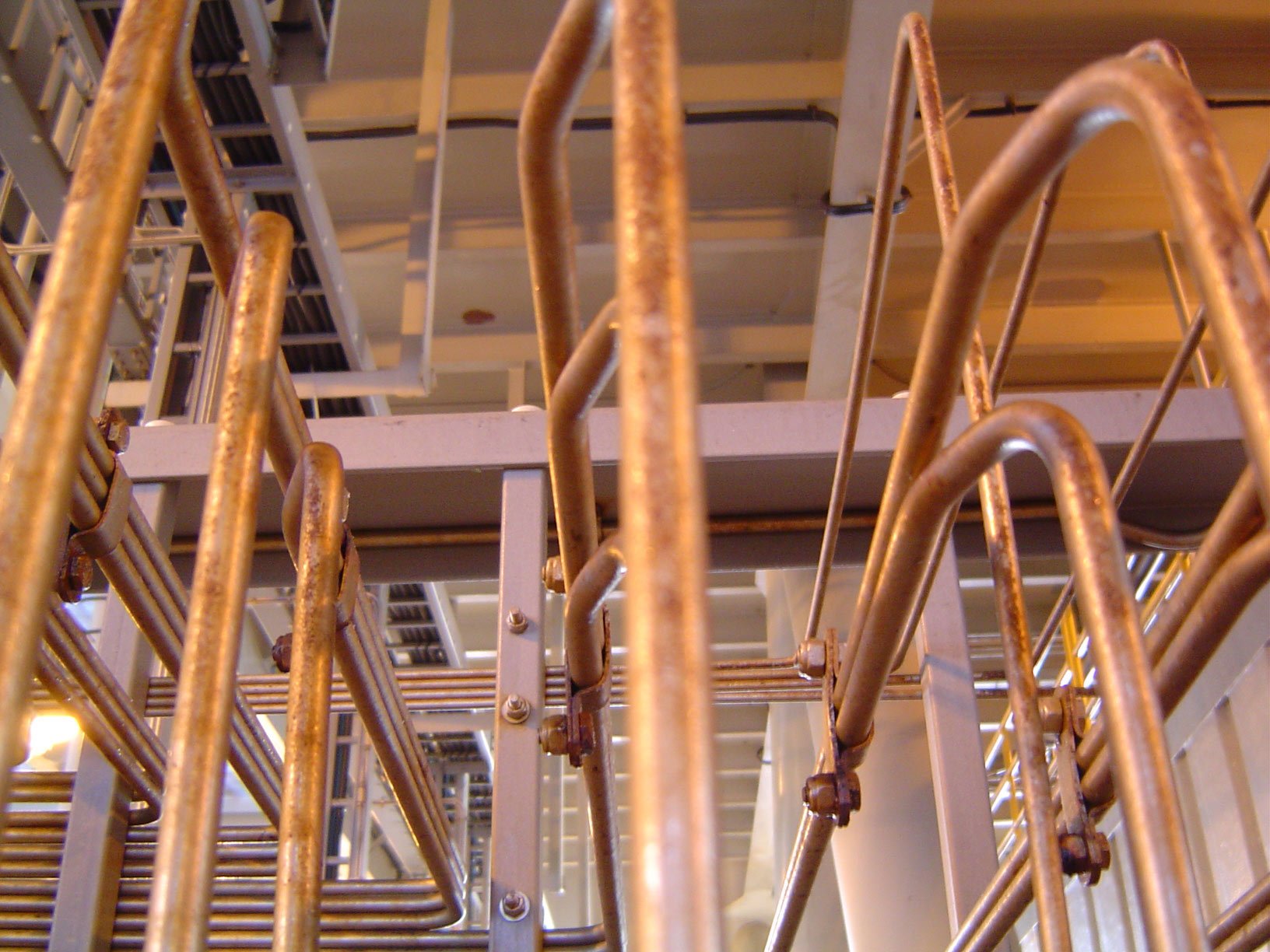
Related Project Experience
A large liquefied natural gas (LNG) producer, with multiple plants along the Gulf Coast, required standard leak testing services during the commissioning and startup phase for their newest plant.
An Independent E&P Company operator’s main 6” infield flowlines on the Gulf of Mexico shelf had been experiencing problematic organic deposition, ultimately rendering it inoperable. The production was re-routed through a parallel 4” line that allowed for production to sustain while the paraffin-stricken line was temporarily abandoned.
A mid-size upstream operator experienced progressively lower flow rates as the result of solids restrictions. Routine pigging procedures were not applicable on the produced water system, as the HDPE product pipe configuration was considered to be unpiggable with conventional methods. This liability reduced the engineering startup flow rates drastically, which initially calculated a rate to move produced water equal to or faster than the production rate. Slower flow rates impeded production and ultimately had a negative reflection for the production asset.
A GoM upstream operator engineered a pre-existing 22” gas pipeline and a pre-existing 8” oil pipeline for common use. This re-engineered scope eliminated CAPEX costs on installing a new pipeline and decommissioning costs on removing the in-service assets by utilizing in-place assets to achieve the new production requirements.
A midstream operator sought flow assurance and integrity services for a gas pipeline with blockage concerns. The unknown location and makeup of the pipeline restriction prevented the operator from performing routine pigging operations. In order to remain compliant with current regulatory standards, a sound remediation method that targeted the blockage area was required in order to successfully plan and execute a hydrostatic pressure test.
An operator of a Liquified Natural Gas (LNG) offshore loading facility required mechanical torque value verification on multiple structural assemblies in order to abide by the manufacturer’s recommended specifications and standards.
An operator of an onshore Liquefied Natural Gas (LNG) micro fuel facility sought integrated solutions from a single source contractor. Ongoing activities with multiple construction groups were working compressed schedules in order to ready the facility for a re-purposed product. Direct technical commissioning support became an value target during the early phase of project execution, as pressure testing and torque value verification for 600+ connection joints demanded specific expertise.
A Gulf of Mexico operator required a safe method to dewater a subsea pipeline upon a recent integrity test. Previous attempts to dewater the pipeline of the hydrotest medium with a foam pig proved unsuccessful. Importantly, the said pipeline was documented to contain heavy paraffin accumulation. Furthermore, the pipeline asset required an application that could mitigate the multi-diameter profile while assuring the client of a complete dewatering task. BlueFin’s casted SoliGel pig was designed to travel throughout the different pipeline diameters while mitigating flow assurance challenges and using production gas as the propelling medium.
A midstream contractor required competent, turnkey commissioning solutions in order to meet an established start-up date. The project consisted of 225 miles of 24 inch NGL pipeline in West Texas. Knowledge of pipeline integrity parameters, SIMOPS scheduling, logistical resources, and proven field personnel were critical to project award approval.
A Gulf of Mexico operator planned a well re-completion of a new reservoir and planned to use an existing flowline. Historical data determined significant paraffin deposition across the flowline. Due to well reservoir modeling analysis, the preexisting flowline warranted an aggressive but confident cleaning program to ensure that the volume capacity was realized.
A pipeline operator required a full line hydrostatic test of a 22-inch crude oil pipeline. The line would be tested in 4 segments. During initial line fill, the pig got hung up and bypassed nearly the entire line fill volume. Once the decision to move forward was made, BlueFin sourced equipment and refilled the line with an alternative water source within 3 days. One segment failed initial test. After repairs, all four segments were successfully tested using electronic data to justify pressure changes.
Startup engineering requirements specified that produced water flow rates should be equal to or faster than the production flowrate. Lesser flowrates would impede production and ultimately create problems in the production schedule and budget. After a considerable production timeline, the operator began to experience severe flow assurance issues on the produced water pipeline as the result of solids buildup.
A major midstream gas transmission company required stress corrosion cracking (SCC) integrity assessment services by hydrotesting to remain compliant with regulatory specifications. The project consisted of a single 101.9 mile pipeline with both 24 inch and 26 inch diameter pipe. Significant environmental hazards were encountered from pipeline contaminants. Additionally, unknown to the pipeline operator, the pipeline contained a significant amount of debris.
A GoM operator of a 6-inch subsea oil production flowline experienced severe paraffin blockage. The said deposition prevented a successful hydrocarbon de-inventory procedure in order to properly abandon the asset per compliance regulations. Due to insufficient pump rates, the operator faced expensive, complex subsea intervention tasks based upon routine flow assurance methods typically applied in decommissioning scopes of work.
An operator of a mini-TLP experienced flow assurance problems in a subsea oil production flowline system. Operator knowledge and production history identified the issue as a paraffin blockage. Unsure of the blockage location and remediation method, several failed attempts at pressure cycling from the subsea and platform sides resulted in a mechanical remediation need.
A GoM operator experienced problematic pressure differentials over a period of time, ultimately resulting in a completely plugged 6” flowline. Heavy paraffin solids completely plugged the flowline and prevented the transportation of liquid product. Upon an evaluation of available remediation methods, an extended reach mechanical solution was selected.
A major midstream operator required decommissioning solutions for an aged gas pipeline asset. In order to properly abandon the said infrastructure in compliance with BSEE and state regulatory departments, engineering managers determined that an inert gas medium would mitigate several risks. As important, the asset contained a large amount of residual liquid product that required safe capture and disposal.
A midstream company required a Department of Transportation (DOT) integrity assessment on a 30-inch transmission gas pipeline. In order to meet federal compliance standards for continued gas operations, the operator elected to execute a hydrostatic pressure test between an existing compressor station and a mainline valve location.
A Gulf of Mexico upstream operator required pipeline abandonment solutions for one 6 inch pipeline. The operator’s permitted Department of Interior (DOI) decommissioning obligation required a seawater flush volume equal to 110% of the internal pipeline capacity.
A major midstream gas transmission company required Stress Corrosion Cracking (SCC) integrity assessment services to remain compliant with regulatory specifications. The pipeline was installed in the 1970s and was located in an environmentally sensitive area with high stakeholder interest and visibility. Further increasing project sensitivity, the pipeline owner expected multiple ruptures during the hydrostatic pressure tests phase. In order to compensate for this risk, an extensive outage period was scheduled and communicated to all customers.
A GoM upstream operator experienced problematic pressure differentials. Over a period of time this resulted in heavy paraffin deposition and ultimately caused several pigs to become stuck in the 6” flowline. Upon an evaluation of available remediation methods, an extended reach mechanical solution was selected to remove the lodged pigs and properly remediate the paraffin deposition.
A GoM operator witnessed a leaking 6” pipeline. Upon repairing the visual leak and attempting to perform a successful hydrostatic pressure test a second non-visual leak occurred, ultimately resulting in extended production loss.
In order to perform a second assessment and bring production back online, the pipeline assessment required a 100% fluidpacked volume of seawater to ensure an oxygen-free environment.
A major midstream gas company required a Stress Corrosion Cracking (SCC) integrity assessment in order to remain federally compliant. The project schedule was of critical importance due to the customer’s demand date for product transmission. This schedule demanded that BlueFin couple engineering subject matter experts and management resources to deliver a work plan that would meet the customer’s deadline.
SafeHeat® technology, custom thermal fluids, and flow assurance engineering provide total approach for plugged GoM pipeline.
Technical expertise and responsive management provide GoM operator with a successful offshore gas pipeline reinstatement.
Integrated mechanical and pipeline services provide bundled solutions for independent GoM operator.
Qualified personnel and responsive management provide gas storage company with multiple SIM OPS pipeline pre-commissioning scopes of work.
Split frame lathe technology delivers field machining solutions for one Supermajor in the Dragon Field block.